Metody
- Značení a použití
- MIG/MAG (CO2)
- MIG pájení (MIG brazing)
- TIG (WIG), PlasmaTIG
- Obalená elektroda (MMA)
- Plasmové řezání
- Více o metodách svařování
Značení metod
Přehled metod značení dle jednotlivých předpisů
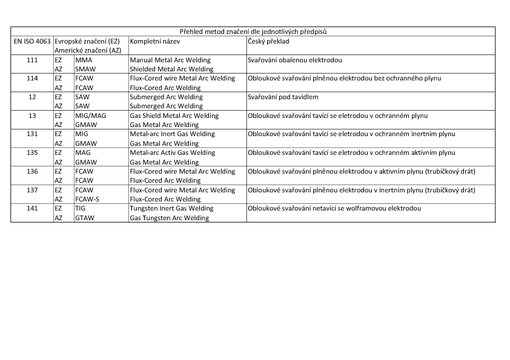
MIG/MAG (CO2)
MIG /MAG svařování
Metoda obloukového svařování tavící se elektrodou v ochranném plynu využívá teplo elektrického oblouku mezi kontinuálně dodávaným drátem (elektrodou) a svařencem. Během tohoto procesu je odtavovaný drát přenášen do místa svařování. Roztavený drát a svarová lázeň je chráněna ochranným plynem. Ochranná atmosféra je dodávána výhradně externím zdrojem a to zásobníkem plynu tlakové láhve nebo rozvod plynu.
Dle složení ochranného plynu pak tuto metodu dělíme na:
· MAG – Metal Active Gas - tedy ochranný plyn aktivní, který chemicky reaguje s roztavenou
lázní O2, CO2 apod.
· MIG – Metal Inert Gas – tedy ochranný plyn inertní, který chemicky nereaguje
s roztavenou lázní jako Ar či He.
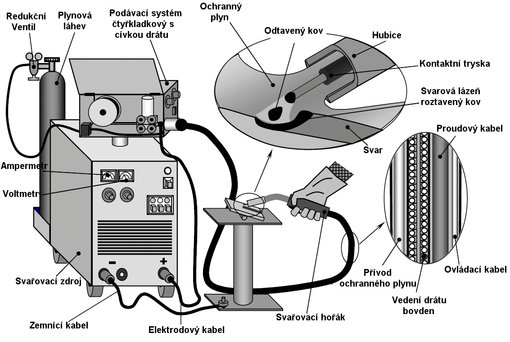
Výhody metody MIG/MAG:
· Svařování ve všech svařovacích polohách
· Vysoká svařovací rychlost = vyšší produktivita
· Odstranění prostoje na výměnu klasických elektrod (MMA)
· Nižší nároky na čištění strusky
· Eliminace zplodin (kouře) oproti metodě MMA
· Oblouk i svarová lázeň je jasně viditelná
· Při svařování ve zkratovém přenosu – nižší vnesené teplo do svařence = menší deformace
Nevýhody metody MIG/MAG:
· Svařovací zdroj je náročnější na obsluhu, pořizovací cena je vyšší.
· Vyšší nároky na údržbu
· Při špatných podmínkách ventilace je riziko odfouknutí ochranného plynu
· Relativně vysoké vyzářené teplo do prostoru
Oblast použití:
· nízko i vysoce legované oceli
· nerezové materiály
· hliník a hliníkové slitiny
· měď a slitiny
Základní aplikační třída použití z hlediska tloušťky materiálu:
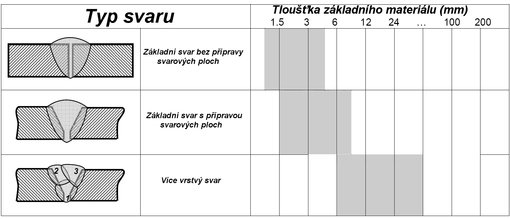
Přenos svarového kovu do svarové lázně:
Velkým přínosem technologie MIG/MAG je schopnost regulovat typ přenosu přídavného materiálu do svarové lázně pomocí vybraných parametrů. Jedná se v podstatě o moderaci odtaveného materiálu (kapky) na základě požadavku nastavených parametrů.
Druhy přenosů:
· zkratový přenos
· kapkový přenos
· impulsní přenos
· sprchový přenos
· moderovaný přenos
· rotační přenos
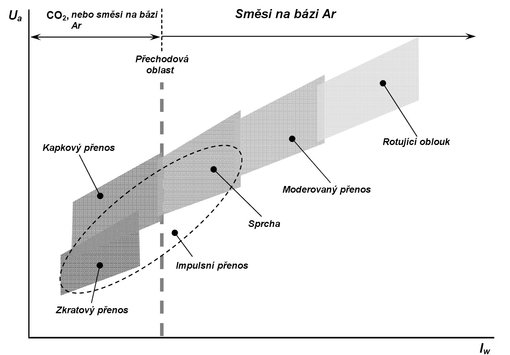
MIG pájení pozinkovaných autokarosářských dílů
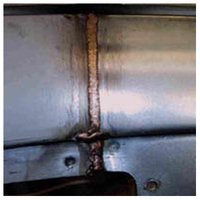
Galvanicky pozinkované plechy jsou stále ve větší míře používány v automobilovém průmyslu.
Jejich svařování je ale problematické, proto je vhodnější metoda MIG pájení, kterou se zachová výhoda odolnosti proti korozi a zabezpečí potřebné mechanické vlastnosti vytvořeného spoje. Protože Migatronic je tradičním dodavatelem svařovacích strojů pro tento obor, rozvíjí i tuto perspektivní metodu spojování kovů.
Při MIG pájení narozdíl od tradičního MIG/MAG svařování dochází k roztavení pouze přídavného materiálu, který procesem blízkým pájení natvrdo spojí nenatavený základní materiál. Nutnými podmínkami této metody jsou stabilní a bezrozstřikový přenos roztaveného kovu a „nízká” teplota oblouku, protože teplota tavení přídavných materiálů používaných při MIG pájení je cca 1060 °C (při běžném MIG/MAG svařování je cca 1650 °C). Díky tomu je minimalizováno teplo vnesené do svařence a možnost poškození vrstvy zinku.
Pro své optimální vlastnosti se dnes při MIG pájení používají zejména bronzové dráty, které při dodržení správného nastavení svařovacích parametrů, ochranné atmosféry a správném vedení hořáku dávají spolehlivý výsledek:
• Koroziodolný svar
• Minimální tepelné ovlivnění
• Minimální odpařování zinku
• Minimální rozstřik
• Minimální nárok na dokončovací operace
• Katodová ochrana základního materiálu v okolí svaru
Protože je teplota tavení přídavného materiálu vyšší než teplota odpařování zinku (cca 910 °C), dochází při MIG pájení k odpařování zinku vždycky. Pokud je ale dodržena podmínka minimální teploty oblouku, udrží se zinek katodickými silami v dostatečném množství v přechodové oblasti mezi housenkou a základním materiálem. Proto je důležité přesné dodržení předepsaných pájecích parametrů svařovacím zdrojem a polohy hořáku obsluhou. Zdokonalení uvedené metody přináší dále použití impulzního svařovacího zdroje, které umožní dokonale naprogramovat celý proces tvorby, oddělení, přenosu a spojení kapky přídavného materiálu pro různé druhy materiálu a polohy svařování. Proto jsou při MIG pájení dosahovány nejlepší výsledky impulzními invertorovými svařovacími zdroji s programovým řízením a pamětí pro individuální nastavení.
Zinek jako antikorozní ochrana oceli je používán pro svou odolnost zachovávat své vlastnosti mnoho let. Velkou výhodou je katodový ochranný efekt, kdy při mírném poškození zinkového filmu dochází k jeho „samoopravení”. Galvanizací je aplikován na ocel ve vrstvě cca 10 – 25 μm.
Právě tloušťka zinku určuje trvanlivost antikorozní ochrany, ale zároveň předurčuje požadavky pro svařování nebo MIG pájení. Kvalita procesu MIG pájení velice záleží na množství odpařených oxidů a zinku, často se mohou objevit póry, průduchy ve svarovém švu, defekty v kořeni svaru, popř. praskliny ve vrstvě zinku. Určujícím parametrem pro správné nastavení procesu je tloušťka zinkové vrstvy. Je-li větší než 15 μm, pak množství a kvalita zinkových par může způsobit nestabilní hoření oblouku. Optimálním řešením je pak použití impulzního oblouku, kde regulací tvaru pulzu docílíme stabilizaci hoření oblouku a odstraníme rozstřik. Výhodou impulsního oblouku je tedy nízká tepelně ovlivněná oblast a tedy i redukce odpařování zinku. Zároveň je zamezeno tvorbě pórů, což je důležité zejména při namáhání materiálu při dalším zpracování nebo při povrchové úpravě.
Rady pro pájení a další informace viz - Ke stažení
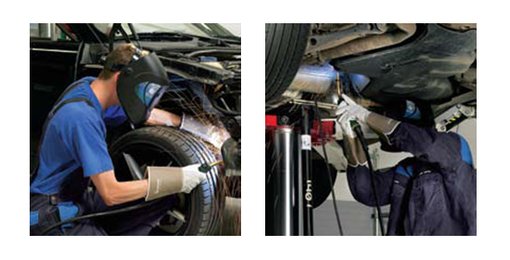
TIG (Tungsten Inert Gas Welding)
Svařování netavící se wolframovou elektrodou pracuje na principu hoření elektrického obloku mezi wolframovou elektrodou a svařencem. Na základě přenosu elektrické energie pak dochází k natavení základního materiálu tedy svařence. Tavící oblouk je chráněn ochranným inertním zdrojem plynu, který zabraňuje vniknutí atmosférických nečistot do svarové lázně.
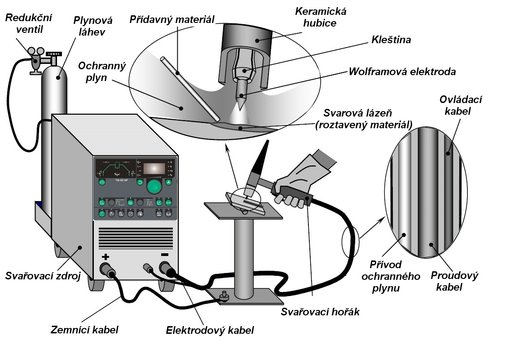
Inertní plyn nebo-li netečný plyn je druh plynu , který nereaguje s dalšími prvky. Plyn do místa svařování proudí a je usměrňován pomocí keramické hubice, kde nahrazuje atmosférický vzduch.
TIG- ové svařování se liší od jiných procesů obloukového svařování tím, že elektroda není „spotřebovávána“ jako elektrody u procesů ostatních MMA či MIG/MAG.
Wolfram je kov s vysokým stupněm teploty tání cca 3300°C, což je v podstatě dvojnásobek teploty tavení oproti klasickým kovům běžně svařitelných.
V případě požadavku na přidání drátu do svaru se používa tzv. přídavný „studený drát“, který lze dopravovat buď ručně, nebo mechanicky.
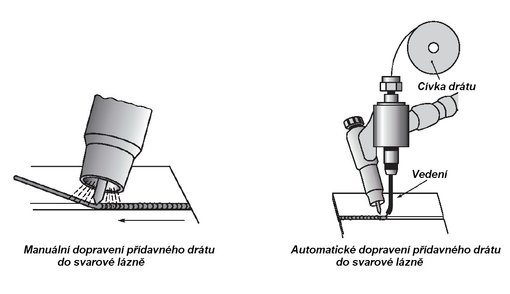
Výhod metody TIG:
· Poskytuje účinnou ochranou svarové lázně v inertním ochranném plynu
· Poskytuje koncentrovaný paprsek
· Je možné svařovat s přídavným drátem i bez něj
· Po svaření není třeba svar dodatečně upravovat jako odstraňovat strusku, kuličky apod.
· Lze svařovat i v místech s nižší dostupností
Oblast použití:
· Lodní průmysl
· Elektrárenský průmysl
· Petrochemický a chemický průmysl
· Potravinářský průmysl
· apod.
Bodování plechů jednoduše
Svařování metodou TIG je vysoce kvalitní způsob spojování kovů. Při běžném TIG bodování jsou ale vzniklé body obvykle nehezké. U běžných TIG svařovacích strojů je proto nutné pro bodování nastavit jiné parametry než pro svařování a svářeč tak ztrácí zbytečně čas změnou nastavení stroje.
TIG-A-TACK™ je nová funkce svařovacích strojů Migatronic Pi pro kvalitní a jednoduché bodování.
Stačí stisknout tlačítko funkce TIG-A-TACK™ na řídícím panelu stroje Migatronic Pi a zdroj změní parametry tak, aby vzniklé body byly malé, pěkné a funkční.
Kvalitní bodový svar vznikne koncentrovanou tepelnou energií TIG oblouku během velice krátkého času. Tím se minimalizuje vnesené teplo a zajistí kvalitní a pohledný bod.
Např. na materiálu tloušťky 0,5 mm hoří oblouk 120 A po dobu 0,03 s. To je výrazný rozdíl proti běžně používaným 50 A po dobu 0,5 s. Proto je vzniklý bodový svar tak kvalitní.
MMA (Manual Metal Arc Welding)
Technologie svařování obalenou elektrodou pracuje na principu hoření oblouku mezi základním materiálem a obalenou elektrodou. Obalená elektroda je složena z plného materiálu tzv. jádra a obalového materiálu.
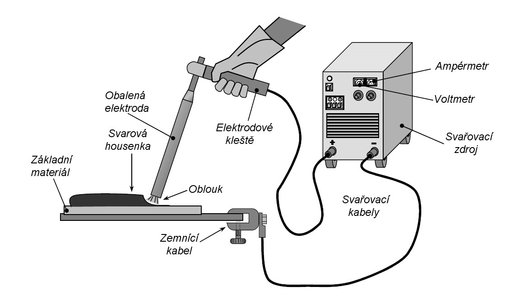
Základní princip:
Oblouk je inicializován v momentě dotyku mezi obalenou elektrodou a základním materiálem (svařencem). Při vzniku obloku dojde k vytvoření svarové lázně. Jádro elektrody pak tvoří nezbytnou složku přídavného materiálu. Další funkční složkou je obalový materiál elektrody, který zabezpečuje ochranu svarové lázně a vytváří tak ochranou atmosféru a strusku. Při procesu chladnutí je svar chráněn povrchovou struskou. Po procesu chladnutí je doporučené strusku odstranit. Obloukové svařování obalenou elektrodou je typický proces pro ruční svařování.
Obalená elektroda disponuje omezenou délkou ( obvykle 350 ..450 mm) to znamená, že proces je často přerušován z důvodu výměny elektrody. Tedy z hlediska produktivity je tato metoda označována právě pro častou výměnu elektrody jako proces s nízkou produktivitou. V poměru je pak produktivita hoření oblouku vyjádřena pouze mezi 20 až 60% z celkového pracovního fondu.
Oblast využití:
Obloukové svařování pomocí obalené elektrody je primárně používáno pro svařování nelegovaný, nízko legovaných i vysoce legovaných materiálů v aplikační tloušťce od cca 2 do 50 mm. Technologie se využívá zejména pro svařování ocelových konstrukcí, tlakové nádoby nebo v lodním průmyslu. Při práci s vyšší sériovostí je třeba použít svařovací procesy, které jsou snadněji mechanizovatelné (např. MIG/MAG)
Základní aplikační třída použití z hlediska tloušťky materiálu:
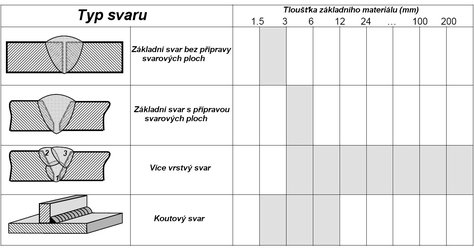
Výhody metody MMA :
· Zařízení pro MMA je relativně jednoduché a přenosné.
· Metoda nevyžaduje externí zařízení plynového hospodářství. Ochrannou vrstvu vytváří obal
elektrody
· Proces je relativně nenáchylný na povětrnostní podmínky jako např. odfouknutí plynu.
· Proces může být použitý i v podmínkách s nižším nárokem na přístup.
· Různorodá použitelnost v oblasti druhů materiálů (uhlíková ocel, slitiny, nerez, litina, hliník
apod.)
· Možnost svařování v polohách.
Nevýhody metody MMA:
· Nutnost odstranění strusky z povrchu materiálu
· Nízká produktivita z hlediska častých výměn elektrod
· Metoda není vhodná na povrchově upravené materiály jako Ti, Zn z důvodu
vysokého vneseného tepla
· Metodu nelze aplikovat na reaktivní prvky, titanium, zirconum, tantalum, columbium z důvodu
reakce a kontaminace kyslíkem
· apod.
Dálkový regulátor FSL na magnetu
Více o metodách svařování
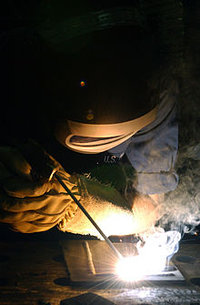
Svařování nebo sváření je proces, který slouží k vytvoření trvalého, nerozebíratelného spoje dvou a více materiálů. Obecným požadavkem na proces svařování je vytvoření takových termodynamických podmínek, při kterých je umožněn vznik nových meziatomárních vazeb.
Protože prakticky je velmi obtížné dosáhnout spojení na úrovni meziatomových vazeb za okolních podmínek (běžná teplota, tlak), kdy je termodynamický stav materiálů stabilní resp. metastabilní, je nutné tento termodynamický stav změnit. Proto je při svařování nutné působit buď tlakem, teplem nebo oběma faktory najednou. Obecně platí závislost čím vyšší působí tlak tím méně je potřeba vnést teplo a obráceně. Tlakové svařování je označením svařování za působení převážně tlaku a tavné při působení tepla.
Svařovat lze kovové i nekovové materiály, materiály podobných i různých vlastností. Ale pro různé typy spojů a materiálů jsou vhodné jiné metody svařování. Při svařování dojde vždy ke změně fyzikálních nebo mechanických vlastností základního materiálu (spojovaného) v okolí spoje. Jiné metody nerozebíratelného spoje jsou např. pájení nebo lepení.
Chcete-li se dozvědět více, klikněte zde
Zdroj informací - Wikipedie
Historie svařování
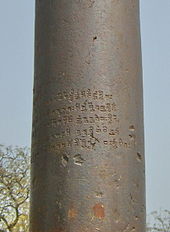
Historii svařování lze datovat již od doby prvních pokusů člověka při tepelném zpracování kovů zhruba k roku 4000 př. n. l. Za jednu z prvních technik tepelného zpracování kovu lze považovat kovářské svařování, při němž se lidstvo seznamovalo s vlastnostmi kovů. Technika kovářského svařování byla používána od nejranějších metalurgických pokusů, výroby zbraní i primitivních nástrojů, vykování Železného pilíře v Dillí, výrobu mečů a dýk z Damascenské oceli a až do 19. století byla jako hlavní a jediná technika pro spojování kovů. Na počátku 19.století byl objeven elektrický oblouk. Ke konci 19. století se začalo rozvíjet svařování plamenem a obloukové svařování, které se stalo ve 20. století dominantní. Urychlení vývoje metod svařování nastalo především během první a druhé světové války. V druhé polovině 20. století byly vyvinuty speciální metody svařování využívající plasmu, laser i elektronový paprsek. Poslední velkou invencí na poli svařování je metoda třecího svařování promíšením vyvinutá v 90.letech minulého století.
Obloukové svařování se začalo vyvíjet až v devatenáctém století po objevu fenoménu elektrického oblouku nezávisle na sobě Angličanem Humprey Davyem (1801) a Rusem Vasilijem Petrovem (1803). V roce 1808 předvedl Humphry Davy hoření elektrického oblouku v Royal Institue v Anglii. Název elektrický oblouk však použil o mnoho let později. Na základě poznatků Humphrey Davyho provedl Angličan Wilde jednoduché spojení dvou kusů železa elektrickým obloukem (1860), pro tento postup mu byl v roce 1865 udělen první patent týkající se svařování kovů za použití elektrického proudu. Teprve až v roce 1881 francouzský vědec Auguste DeMeritens použil, pravděpodobně jako první, elektrický oblouk jako takový při svařování olověných desek uhlíkovími elektrodami. Uhlíkovou elektrodu připojil na záporný pól a svařované předměty na kladný, tzv. přímé zapojení. Pro svůj postup si nechal ve Francii vydat patent. Jako zdroj elektrického proudu posloužily akumulátorové baterie. Proces svařování holými kovovými elektrodami nebyl dostatečně efektivní při zvyšující se průmyslové potřebě. Pro zvýšení kvality svarů - zejména tažnosti - byly vyvinuty elektrody s kovovým jádrem a boalem z prvků a sloučenin, které zvýšily ochranu svarového kovu, pomohly při rafinace svarového kovu a zvýšily stabilitu hoření elektrického oblouku. Právě Oscar Kejllberg, zakladatel švédské firmy Esab, v roce 1907 opatřil kovovou odtavující se elektrodu obalem z uhličitanů a křemičitanů, tzv. obalovaná elektroda a svůj vynález si v témže roce nechal patentovat. Výsledky jeho práce se využívají více než 100 let až do dnešní doby jakoruční obloukové svařování obalenou elektrodou.
Firma Lincoln Electric Company představila v roce 1912 po pětiletém vývoji vlastní svařovací zařízení.
Ve Velké Británii Arthur Percy Strohmenger experimentoval v letech 1909 až 1912 s tlustými obaly kovových elektrod, používal širokou škálu materiálů od azbestové tkaniny až po jíl a vápenec. Výsledek své práce si nechal patentovat v USA až v roce 1928. Teprve při použití jeho elektrod bylo konečně možné svarový kov provést ve vysoké kvalitě bez jakýchkoliv nečistot. Obalované elektrody si hledaly dlouhou cestu ke svářečům, na vině byla jejich cena způsobená nákladným technologicko-výrobním postupem. Ke zlevnění došlo až po změně technologie výroby kovového jádra elektrody tažením a zároveň průtlačného lisování použitého při výrobě jejího obalu.
Během první světové války byly kladeny zvýšené požadavky na vývoj nových postupů svařování v souvislosti se zbrojní výrobou. Z důvodu nedostatku plynu Angličané nepoužívali při opravách lodí a výrobě zbraní běžné svařování plamenem, ale byli nuceni použít metodu obloukového svařování. Rychlá oprava poškozených zařízení za pomoci obloukového svařování přesvědčila mocnosti o přednostech této svařovací metody. Jedním z klíčových momentů pro následující vývoj obloukového svařování byla práce Paula O. Nobleho, který si nechal v roce 1924 patentovat svůj postup svařování stejnosměrným proudem za použití svařovacím napětím ovládaného podávání svařovacího drátu.
V roce 1928 v East Pittsburghu byl přes Turtle Creek (tj. Želví potok) postaven první celosvařovaný most v USA společnými silami firem WestingHouse Electric a Manufacturing Company. Most byl dlouhý 18,6 m a vážil cca 10 tun. Ve stejném roce se ve Vítkovických železárnách začaly vyrábět první obalované elektrody máčením.
V tehdejším Československu bylo svařování využíváno pro výstavbu tlakových nádob i mostů již v meziválečné době. Na počátku třicátých let 20. století byly v Plzni postaveny dva svařované mosty. První, který byl postaven v roce 1931 ve Škodových závodech přes železniční trať, byl svařován holými elektrodami. Druhý, dnešní Tyršův most přes řeku Radbúzu, byl postaven o dva roky později. Se svým rozpětím 49,2 m byl v té době největší na světě. Autorem obou mostů byl významný český propagátor svařování, inženýr a později profesor ČVUT v Praze František Faltus. V roce 1949 byl Jozefem Čabelkou založen v Bratislavě mezinárodně uznávaný Výzkumný ústav zváračský.
Chcete-li se dozvědět více, klikněte zde
Zdroj informací - Wikipedie
- Tyršův most z roku 1933
- Novinky
- Tipy, rady, doporučení
- Autoopravárenství
- Svařování ve výrobě
- Automatizace
- Robotizace
- Ocenění / Napsali o nás
- Výstavy